- Главная
- Сварка стали
Сварка стали, технология и способы сварки стали
Компания Argoniks выполняет услуги по сварке стали любого типа и марки ГОСТа. Качественные соединения разнородных сталей с применением аргонодуговой сварки. Работаем с металлами различных марок, включая сварку стали 40х, 30хгса, 20к и других видов. Ремонтируем и изготавливаем под заказ торговые, строительные, лестничные, решетчатые и другие конструкции,а также детали любого назначения. Низкая стоимость услуг! Быстрый выезд специалиста! Гарантия на проведение сварочных работ!
Содержание:
-
Технология сварки стали с низким содержанием углерода
-
Технология сварки разных типов конструкционной стали
-
Особенности сварки конструкционных материалов
-
Технология сварки разных видов легированной стали
-
Технология сварки различных типов низколегированной стали
-
Технология электрошлаковой сварки
-
Технология сварки стали различных структурных классов
-
Технологии сварки разнородных типов стали одного структурного класса
-
Электроды для сварки конструкционных сталей
-
Технология сварки двухслойных (плакированных) видов стали
-
Как свариваются низколегированные стали
Технология сварки стали с низким содержанием углерода
В составе инструментальной стали присутствует до 1 % углерода, что определяет ее твердость и прочность. В то же время износостойкость металла достаточно низкая, поэтому из него изготавливают только инструменты. А невысокая закупочная цена обеспечивает прибыльность производства.
Технология сварки стали этого типа предполагает использование инвертора и специально предназначенного электрода. Для обработки подходят стержни УОНИ-13/НЖ/20Х13 и сварочный инвертор.
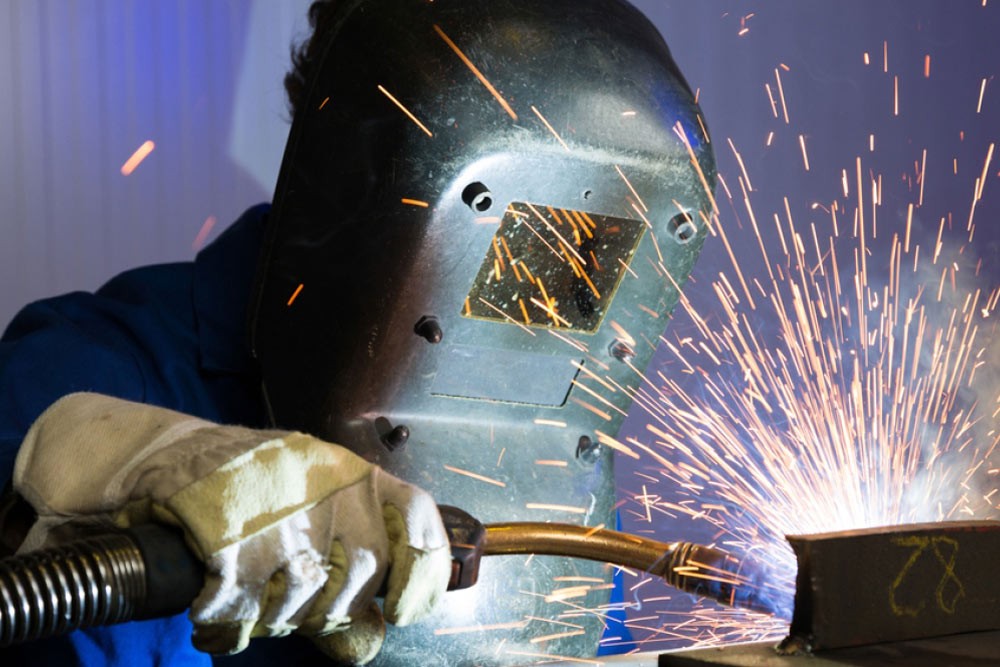
Технология сварки разных типов конструкционной стали
Более востребованной является конструкционная сталь, она используется для производства как мелких металлических деталей, так и габаритных станков. В эту категорию входят стали таких марок, как 40х, 30хгса, 35хгса и др.
В составе конструкционной стали присутствуют различные примеси, включая серу и фосфор. Большее количество этих компонентов уменьшает надежность материала.
Конструкционные типы стали делят на несколько групп:
обыкновенная;
качественная;
высококачественная;
особо высококачественная.
В последней группе присутствует минимальное количество примесей, поэтому сталь является наиболее прочной и качественной. Обычная конструкционная сталь, напротив, содержит высокий процент примесей, поэтому долговечностью не отличается. В названных группах существует деление на подгруппы в зависимости от присутствия в составе дополнительных химических элементов.
Особенности сварки конструкционных материалов
Конструкционная сталь включает в себя углеродистую сталь и легированную сталь. Количество легирующих элементов в конструкционной стали не превышает 5%.
Воздействие углерода и легирующих элементов может быть аппроксимировано углеродным эквивалентом где С, Mn, Ni, Cr, Mo, V — пропорции химических элементов.
По химическому составу все конструкционные стали отличаются свариваемостью и могут быть разделены на четыре группы, которые требуют различных условий сварки для обеспечения надежных и равных по прочности сварных соединений.
К ним относятся низкоуглеродистые стали с содержанием углерода менее 0,25% и низколегированные стали с содержанием углерода менее 0,2%. Эти стали свариваются без трещин при температуре окружающей среды до –20 ° С.
Не требуется термическая обработка после сварки.
Однако это исключает структуры, которые не могут допускать коробления или поводка во время обработки и эксплуатации.
В эту группу входят стали:
- Ст1 … Ст3;
- 08, 10, 15, 20, 25;
- 15Л, 20Л; 15Г, 20Г, 15Х, 20Х, 15Н2М, 12ХН2, 09Г2, 16ГС, 10Г2С1Д и другие группы II.
Полностью сварная сталь с содержанием углерода или эквивалентом в диапазоне 0,25 … 0,35%. Эти стали свариваются без дефектов при температуре окружающей среды выше 5 ° C.
В противном случае, если толщина детали превышает 25 мм, перед сваркой ее следует нагреть до 50-100 ° C. После сварки рекомендуется термообработать конструкцию, особенно толстую.
Примеры сталей из этой группы:
- Ст5, Ст5Г,
- 30, 35,
- 20ХНЗА, 30Л, 35, 27ГС, 20ХГС,
- Другие группы III
Сварочные предельные значения стали, эквивалентное или абсолютное содержание углерода составляет 0,35-0,45%.
Чтобы обеспечить высокое качество сварных швов, эти стали необходимо предварительно нагреть перед термообработкой до 100-200 ° C и подвергнуть термообработке после сварки. Термическая обработка — это либо отжиг, либо закалка с последующим высоким отпуском.
Ограниченные свариваемые группы включают в себя такие стали, как Ст6, 40, 45, Сталь 30ХМ, 30ХГСА, 20Х2Н4А. Группы IV — плохо сварные стали с содержанием углерода более 0,45%.
Для сварки предварительно нагреть до 250-350 ° C и после сварки требуется термообработка.
- Стали 45Г, 40Х, 65Г, 40ХН, 60СГА, 38Х2МЮА, У7 и т. Д. Плохо свариваются, температура нагрева стали удовлетворительная, ограниченная, плохо сваривается, а зона термического влияния легко затвердевает, Эмпирическая зависимость 350 C 0, 25 Tp = ЭS-, (2) Tp — температура нагрева деталей перед сваркой, ° С. CSS является углеродным эквивалентом с учетом химического состава стали и толщины детали: Где C, Ni, Mn, Cr, пропорции Мо-химического элемента; толщина S-связанного компонента, мм.
Технология сварки разных видов легированной стали
Самыми востребованными являются различные виды легированной стали. Спрос на них обусловлен составом, в который включены различные легирующие компоненты, придающие металлу нужные характеристики и свойства.
Добавки придают металлу повышенную прочность, долговечность, улучшают его характеристики. Физико-химические свойства материала меняются путем добавления в состав легирующих компонентов.
К достоинствам разных типов легированной стали также относятся:
- высокая жаропрочность;
- устойчивость к коррозии (сравнивать их с нержавеющей сталью, конечно, нельзя, однако они обладают повышенной стойкостью).
Технология сварки стали этого типа предполагает использование дугового метода обработки и электродов с фтором и кальцием. Оптимальным вариантом является применение газовой сварки, качество соединения деталей в этом случае получается более высоким.
Разница в технологии сварки стали газом и полуавтоматом или инвертором заключается в образовании тепла за счет пламени газовой горелки, а не электрической дуги. Пламя возникает при смешивании горючего газа с кислородом. Для использования технологии газовой сварки углеродистых сталей необходимы опыт и сноровка.
Технология сварки различных типов низколегированной стали
В составе разных типов низколегированной стали (чаще всего они же являются низкоуглеродистыми) присутствует небольшой процент легирующих компонентов (в основном, в пределах 2-3 %). В составе этих металлов есть железо, небольшой процент углерода и различные примеси.
Низколегированная сталь, устойчивая к высокотемпературному воздействию (до +200 °С), используется для производства хирургических, ювелирных, гравировальных инструментов, бритв и лезвий. Добавление небольшого количества хрома в состав позволяет получить металл, отличающийся высокой прочностью и долговечностью.
Низколегированная сталь входит в класс черных металлов, используется для производства габаритных сварных металлических конструкций. Хотя содержание легирующих компонентов в ее составе невелико, материал обладает высокой прочностью. Такие характеристики достигаются за счет присутствия в составе хрома, никеля и молибдена, улучшающих свойства низколегированной стали. Благодаря хрому и никелю повышается устойчивость металла к коррозионному воздействию.
Соблюдение технологии сварки стали этого типа позволяет достичь хороших результатов. Однако при работе с низколегированными металлами необходимо учитывать многочисленные особенности материала. Большую роль играет опыт сварщика.
Чаще всего мастера сталкиваются с перегревом сварной области. Такая проблема возникает при работе с различными марками низколегированных сталей. Из-за быстрого охлаждения сварного шва и заготовки в целом на месте соединения образуется мертенсит. Так называют твердую углеродистую структуру, возникающую на сварном шве из-за резкого охлаждения.
Технология сварки стали с низким содержанием углерода предполагает использование электродов с кальцием и фтором. Наиболее подходящими являются стержни, имеющие основное покрытие, такие как Э42А или Э50А. Лучшими считаются электроды марок УОНИ 13/45, МР-3, АНО-8, СМ-11. Впрочем, подойдут и другие, обладающие похожими характеристиками.
Технология сварки стали с низким содержанием углерода позволяет пользоваться полуавтоматической или автоматической сваркой под флюсом с полуавтоматом и присадочной проволокой. Флюс может быть заменен углекислым газом или смесью углекислого газа и аргона. Это позволяет повысить качество шва по сравнению с работой с электродами.
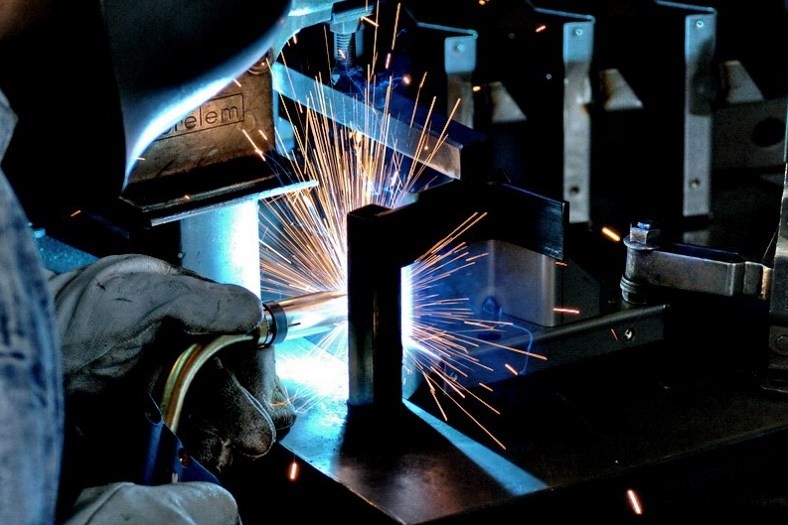
Технология электрошлаковой сварки
Из углеродистых литых сталей марок 25А и 35А (ГОСТ 977) с помощью электрошлаковой сварки изготовляют такие изделия, как станины прокатных станов (рис. 143), архитравы мощных гидропрессов (рис. 144), бандажи цементных печей (рис. 145), ползуны механических ковочно-штамповочных прессов, плиты рольгантов и другие детали прокатного оборудования.
Рис. 143. Станина прокатного стана, сваренная электрошлаковым способом.
В станинах прокатных станов свариваемое сечение имеет небольшую высоту при довольно значительной ширине. Поэтому электрошлаковую сварку станин в большинстве случаев выполняют пластинчатыми электродами. В качестве электродного металла применяют марганцевую сталь 09Г2 (ГОСТ 5058) или другую низколегированную сталь с малым содержанием углерода, например, 10Г2СД, 10ХСНД и 10ХГСНД.
Эти стали легируют металл шва марганцем, кремнием и хромом и тем самым придают ему требуемые механические свойства при значительно меньшем содержании углерода, чем в свариваемом металле. Последнее обстоятельство имеет весьма важное значение, так как уменьшает вероятность появления трещин в металле шва.
Соединение с шириной сечения от 450 до 750 мм, сваренное на таком режиме, получается без непроваров, трещин и других макродефектов. После сварки станины подвергают нормализации с последующим отпуском.
В некоторых сварнолитых изделиях свариваемыми сечениями являются прямоугольники с довольно большой высотой и сравнительно небольшим основанием. В этом случае электрошлаковая сварка выполняется тремя электродными проволоками, перемещаемыми по толщине свариваемого металла.
Если толщина свариваемого металла более 400 мм, то электрошлаковая сварка выполняется четырьмя или шестью проволоками с двух сторон, т. е. двумя аппаратами, один из которых устанавливается на лицевой стороне соединения, а другой — на тыльной. Аппараты настраиваются на синхронную работу в течение всего процесса сварки.
Несколькими проволоками могут быть сварены, например, ползуны механических ковочно-штамповочных прессов, бандажи цементных печей и архитравы мощных гидравлических прессов.
Технология электрошлаковой сварки ползунов ковочно-штамповочных прессов аналогична технологии сварки кованой стали 35, предусматривает предварительный подогрев места сварки до 150—200°С и применение электродной проволоки Св-10Г2. Режим сварки указан в табл. 97. Сваренный ползун подвергается нормализации с последующим отпуском.
Сложнее сваривать бандажи цементных печей, представляющие собой толстостенное кольцо. Размеры этого кольца настолько велики, что оно изготовляется в виде двух полуколец, свариваемых при монтаже печи.
Бандаж сваривается после механической обработки, поэтому необходимо принимать меры, ограничивающие его деформацию в пределах допустимых величин. Основными способами ограничения деформаций являются одновременная сварка обоих стыков и правильный выбор ширины зазора между свариваемыми кромками.
В остальном технология электрошлаковой сварки бандажей цементных печей ничем не отличается от технологии сварки ползунов ковочно-штамповочных прессов.
Бандажи цементных печей начали сваривать плавящимся мундштуком, который состоит из стальных пластин (МСтЗ или МСт4 по ГОСТ 380) толщиной 5 мм и спиралей из проволоки Св-10Г2.
Толщина бандажей современных цементных печей 290 и 350 мм, поэтому сваривают их мундштуком, по которому подается четыре электродные проволоки. При этом применяется следующий режим сварки:
Сварочный ток, А 1800—2200
Напряжение сварки, В 46—48
Глубина шлаковой ванны, мм 30—35
Архитрав современных мощных гидропрессов является крупнейшей сварнолитой деталью, изготовляемой с применением электрошлаковой сварки.
Масса отливки этой детали около 300 т. Сварнолитой архитрав состоит из двух частей, соединенных между собой пятью швами. Толщина свариваемого металла составляет 260, 365 и 400 мм, в связи с чем сварку архитрава рекомендуется выполнять на следующем режиме:
Количество электродов, шт 3
Сварочный ток на одном электроде, А 400—500
Напряжение сварки, В 50—52
Скорость поперечного перемещения электродов, м/ч 39
Глубина шлаковой ванны, мм 40—60
Сварка выполняется проволокой Св-10Г2.
Архитрав отливается из стали 35Л. Высокое содержание в стали углерода, а также весьма большая жесткость конструкции заставляют применять при сварке предварительный подогрев, а после сварки — немедленную нормализацию с последующим отпуском.
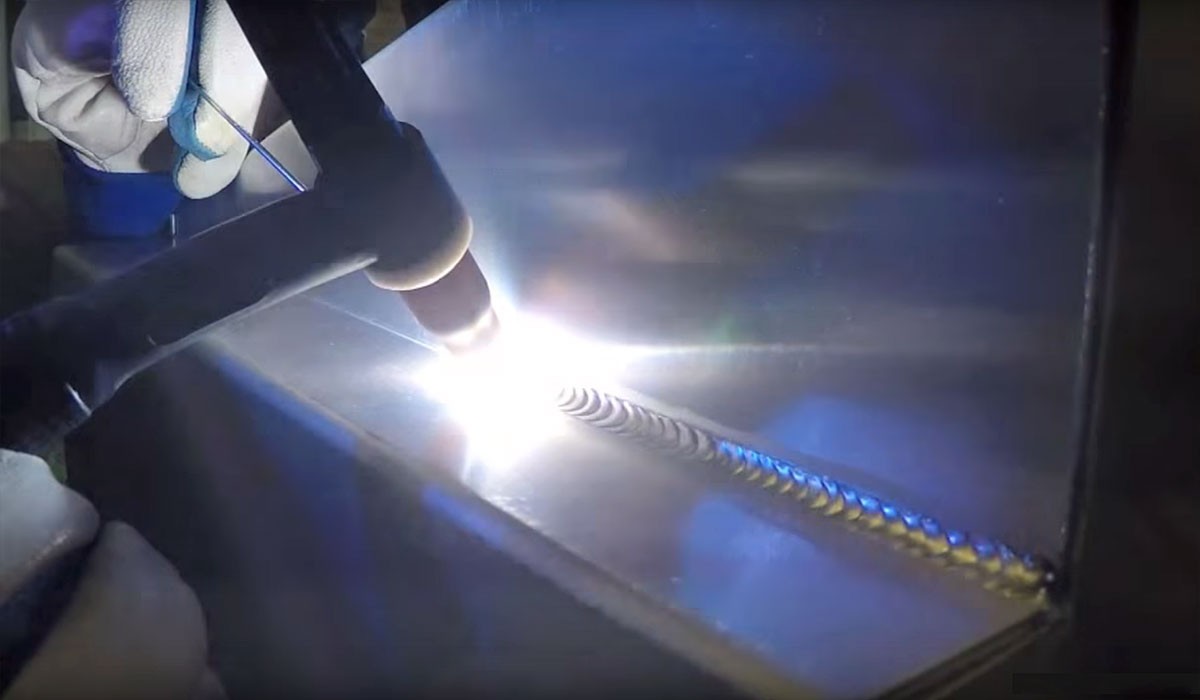
Технология сварки стали различных структурных классов
Перлитную и аустенитную стали сваривать сложнее, поскольку на сварном шве образуются мартенситный налет или карбидная гряда, причем их объем снижает степень легирования материала, приближая его к характеристикам перлитной стали. Прослойка образуется в связи с худшим перемешиванием жидкого металла в пристеночных слоях. Если запас аустенитности металла в районе шва невелик, то прослойка может достигнуть критического уровня, приводя к разрушению соединения.
Соответственно, выбирая технологию сварки стали, необходимо отдавать предпочтение той, которая позволят добиться минимальной толщины кристаллизационного слоя. Для этого:
- используют высококонцентрированные источники тепла, например, электронный луч, лазер, плазму;
- разделывают или наплавляют кромки, снижая содержание участвующих в процессе сталей;
- выбирают режимы обработки, при которых толщина плавления минимальна;
- используют дуговую сварку в защитной газовой среде, способной обеспечить интенсивное смешивание металла сварной ванны.
Для сварки комбинированной стали наиболее подходящей является обработка в защитной газовой среде, поскольку при использовании этой технологии повышается температура расплавленного металла, снижается поверхностное напряжение, а значит, повышается интенсивность его смешивания. Это обусловлено увеличением приэлектродного падения напряжения сварочной дуги и кинетической энергии переноса капель металла электрода и плазменного потока в сварочной дуге.
Усилению эффекта способствует добавление в аргон кислорода, азота, углекислого газа. При добавке кислорода увеличивается температура в сварной ванне, а также возникают экзотермические окислительно-восстановительные реакции. За счет этого уменьшается степень структурной и механической неоднородности в области соединения перлитного металла с аустенитным швом.
Ручная дуговая технология сварки стали позволяет добиться лучших результатов в случае уменьшения температуры плавления электродов и, как следствие, температуры сварной ванны. Чтобы уменьшить температуру плавления электродов, используют стержни, в составе которых присутствуют никель и марганец. При применении этих электродов в процессе сварки под флюсом уменьшаются также кристаллизационные и диффузионные прослойки.
СВАРКА ЗАКАЛЕННОЙ ЛЕГИРОВАНОЙ СТАЛИ 40ХН
При изготовлении сварных конструкции необходимо решать, как правило две задачи; обеспечение требуемых техническими условиями механических свойств и предупреждения образования дефектов в сварных соединений. Наиболее опасными и недопустимыми дефектами являются трещины. Трещины возникают в швах при его кристаллизации (горячие трещины)и в околошовной зоне (холодные трещины) Сварные конструкции могут быть изготовлены из проката, отливок или поковок., прошедших перед сваркой операцию изотермического отжига. Имеется достаточно большое количество информации, касающейся образованию горячих и холодных трещин при дуговой сварке в сварных изделиях выполненных из заготовок, прошедших предварительную термическую обработку (отжиг) В некоторых случаях, когда от детали, по условиям работы, требуется высокая твердость, обеспечиваемая закалкой. приходится сваривать предварительно закаленную заготовку…
В связи с задачей изготовления сварных цилиндров из плохо сваривающейся стали 40Х целью настоящей работы стояла изучение свариваемости ее в закаленном состоянии и разработка технологии дуговой сварки этой стали со сталью 20
Для решения этой задачи в качестве пробы был выбран один из узлов , воспроизводивший форму и размеры натурного сварного соединения. и подвергающийся после сварки – термообработке закалке с отпуском .Проба состояла из цилиндрического корпуса стали 40Х с внутренней резьбой, в который ввертывалось донышко из стали 20 и обваривалось по периметру кольцевым швом (рис.1)
1 – сварной шов; 2 – донышко; 3 – цилиндр.
Рис.1. Сварной образец для определения свариваемости стали 40Х:
Перед сваркой, для получения требуемой твердости Н =2860-3020 МПа образец подвергали термической обработке закалке с отпуском по режиму приведенному на рис.2
Микроструктура образца перед сваркой представляла сорбитообразный перлит. Приварку донышка производили следующим образом.
Рис.2 -График термической обработки пробы
Деталь подвергали общему нагреву в электропечи до температуры 350-400 0С, затем производили сварку в нижнем положении, в два слоя с обязательной послойной зачисткой шва от шлака по режиму :сила сварочного тока–160–200 А; род тока–постоянный, полярность –обратная. При сварке использовали сварочные материалы:электроды УОНИ 13/55, тип электрода – Э50А, диаметр электрода–4 мм, катет шва-8 мм.
После сварки образец охлаждали вместе с печью. и контролировали. В результате просвечивания сварных швов рентгеновскими лучами дефектов не было обнаружено. Проверка наружной поверхности швов путем шлифовки с последующим травлением кислотой показала, что поверхностные трещины также отсутствуют. Для определения качества сварного соединения были изготовлены макрошлифы.
В результате проведенного макроисследования выявлено плотное строение наплавленного металла сварного шва и околошовной зоны. Микроструктура зоны наплавленного металла – феррито-перлитная; околошовной зоны – сорбитообразный перлит.
Сварные образцы прошли испытание на твердость Результаты испытаний показали, что сварка закаленной стали 40Х по указанной технологии не изменяет структуру и твердость основного металла. в зоне термического влияния (рис.3. т.3 и 6)
1-7 – точки замера твердости
Рис. 3 График замеров твердости сварного образца:
Результаты исследования сварки закаленной легированной стали 40Х позволили применить ее при изготовлении цилиндров.
Технологии сварки разнородных типов стали одного структурного класса
Сварка разных типов перлитной стали, разница в которых заключается в степени легирования, выполняется с помощью электродов, используемых для металлов с меньшей степенью легирования, при отсутствии дополнительных требований к прочности соединений, жаропрочности, коррозионной устойчивости, которые свойственны более легированным сталям. При этом технология предполагает выбор режимов и температуры сварки, применяемых при работе с более легированными металлами.
Если подогрев невозможен, то выполняется наплавка кромок с использованием более легированного материала, подогреваемого электродами типа Э42А. При этом наплавленный слой должен иметь такую толщину, которая не позволит более легированному металлу нагреться до температур Ac1, т. е. не допустить создания условий для закалки.
Работая с различными сочетаниями высокохромистых мартенситных (12 % Cr), ферритных (28 % Cr) и ферритно-аустенитных металлов типа Х21Н5, необходимо выбирать такую технологию сварки сталей, при которой не будут образовываться холодные трещины и хрупкие участков в сварном шве. Режим подогрева выбирают для самого закаливающегося металла с недопущением полного охлаждения заготовок. Это возможно при использовании сварочных материалов ферритно-аустенитного класса, сварки с минимальной погонной энергией, поскольку металлы с высоким содержанием хрома подвержены росту зерна, являющегося причиной образования хрупкости места шва.
После того как термообработка завершена, заготовку необходимо быстро охладить, чтобы избежать хрупкости, возникающей при +475 °С. Можно также использовать для работы аустенитные электроды. Но в таком случае при термообработке нельзя полностью исключить сварочные напряжения, вызванные разницей в коэффициентах линейного расширения шва и основного металла.
Электроды для сварки конструкционных сталей
Подобная склонность к образованию дефектов сварки объясняется повышенным содержанием углерода, поэтому существенно усложняются работы по соединению таких металлических сплавов. В данном случае можно использовать электроды, которые по своим характеристикам максимально приближены к основному сплаву. Также возможно использование сварочной проволоки.
Выбор диаметра электрода в данном случае зависит от толщины металлического сплава. При этом можно использовать электроды с толщиной от 1,5 до 6 миллиметров. Соответственно показатели сварочного тока колеблются от 20 до 240 Ампер.
В том случае, если проводится работа с толстыми листами, возможно выполнение многослойной сварки, когда каждый последующий слой выполняется через небольшой промежуток времени. Для устранения так называемых закалочных структур рекомендуется проводить дополнительную термообработку. Для этого необходимо нагреть изделия до температуры более 600 градусов и выдерживать такую температуру в течение нескольких часов, после чего охлаждать на открытом воздухе или в воде.
Обработка низколегированной конструкционной стали может выполняться в защитном газе полуавтоматической и автоматической сваркой. При использовании технологии электрошлаковой сварки можно использовать проволоку марки Св-о8Г2С. Для защиты используют дополнительный флюс АН8.
Технология сварки двухслойных (плакированных) видов стали
За счет двухслойной стали снижается использование высоколегированных материалов, при этом работоспособность конструкций не снижается. Из таких металлов изготавливают оборудование, эксплуатируемое в коррозионной среде.
Облицовочный слой толщиной до 12 мм, устойчивый к коррозии и контактирующий с агрессивной средой, выполняется из следующих металлов:
- высоколегированных хромоникелевых аустенитных (12Х18Н10Т, 08Х18Н10Т, 12Х18Н12Т, 08Х18Н12Б и др.);
- хромистых ферритных;
- мартенситно-ферритных (08X13, 12X13 и др.).
Основной слой, толщина которого достигает 150 мм, более устойчив к силовым нагрузкам. Для его изготовления используются углеродистые низколегированные металлы (Ст3, 20К, 15ХМ и др.). Сварные соединения при этом должны иметь:
- Однородность облицовочного слоя с высокой коррозионной стойкостью сварного шва.
- Отсутствие комплексных сплавов с низкими механическими характеристиками в месте соединения облицовочного и основного слоев. Для этого необходимо использовать подходящие материалы и технологию сварки сталей, разделывать кромки и последовательно проводить работы.
Описанию основных типов и конструктивных элементов формы подготовки кромок в соответствии с технологией и способами сварки посвящен ГОСТ 16098-80. Сварка слоев выполняется раздельно с применением различных сварочных материалов. Последним обрабатывается облицовочный слой, чтобы не допустить его повторного нагрева. Обработка основного покрытия осуществляется в первую очередь. Для работы используются подходящие сварочные проволоки, флюсы, электроды и пр.
Как свариваются низколегированные стали
Для низколегированных конструкционных сталей подходит и автоматическая, и ручная сварка. Качество шва и простота проведения процедуры тесно связаны с характеристиками свариваемого материала. На эти параметры напрямую влияет количество углерода — чем оно ниже, тем качественнее шов и легче выполняется процедура. Наилучший результат получается при сваривании марок стали, устойчивых к появлению трещин в сварном соединении и неподверженных закаливанию.
При автоматической сварке применяется сварочная проволока и дополнительный флюс, который обеспечивает защиту обрабатываемого участка. Ручная выполняется при помощи электродов. При сварке листов толщиной менее 4 см кромки разделывать не обязательно.
Если сварочные работы проводятся с низколегированными сталями на основе хрома, кремния и марганца, то следует учесть, что они склонны к образованию закалочных участков и трещин в области шва. Вероятность их появления тем выше, чем тоньше кромки листа.